Rispetto ai diversi tipi di manutenzione (a guasto, preventiva, programmata, predittiva) la gestione della manutenzione è un’attività spesso considerata poco redditizia per l’azienda. Tante sono le politiche di manutenzione possibili, ognuna con punti di forza e di debolezza. In questo articolo spieghiamo come fare per scegliere il corretto piano di manutenzione aziendale più adatto alle proprie esigenze.
Negli ultimi anni i sistemi produttivi sono sempre più focalizzati a massimizzare la loro efficienza. L’avvento della Lean Production e, successivamente, del WCM hanno portato le aziende a considerare le attività di manutenzione non più come un peso ma come un servizio alla fabbrica. Non stupisce quindi come le aziende siano diventate più sensibili quando si parla di questo argomento poiché ci si è resi conto di come un'attenta gestione della manutenzione del sistema produttivo porti più benefici al sistema stesso nel suo complesso di quanto si possa pensare e come questa rappresenti un pilastro per il miglioramento del Operations Management. Per fare qualche esempio di effetti benefici di una buona e costante attività di manutenzione dei sistemi produttivi possiamo pensare alla riduzione dei fermi linea o all’affidabilità degli impianti in termini di velocità (evitando microfermate e rallentamenti) e di qualità (numero di scarti minimo).
Per scegliere una strategia, occorre disporre di elementi oggettivi che indirizzino la scelta. Ecco quindi un ragionevole punto di partenza: mettere sotto controllo il processo di gestione della manutenzione aziendale.
Ma come fare?
Pensiamo che attraverso l’esempio di un caso reale sia più semplice capirlo.
Nell'ambito di un progetto di consulenza, ci è stato chiesto di aiutare un’azienda a migliorare, in generale, il suo processo di manutenzione. In questo caso ci siamo concentrati sul reparto di confezionamento, organizzato per linee, dove la complessità nasceva dalla varietà di macchine e tecnologie presenti. Il primo passo è stato quello di analizzare lo stato dell'organizzazione attuale per capire quali persone erano coinvolte nel processo, quali erano le loro competenze, quali procedure venivano adottate e quali strumenti avevano a disposizione. I risultati dell'analisi hanno messo in luce alcune criticità su vari aspetti.
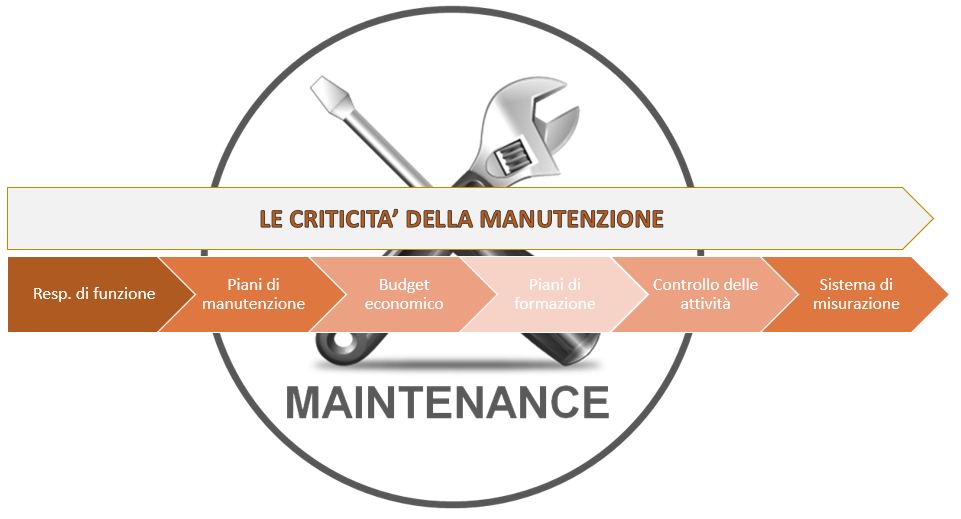
Un elemento di debolezza era sicuramente rappresentato dalla mancanza di un responsabile della manutenzione; erano presenti due referenti che però non si preoccupavano di seguire l’organizzazione del processo. Erano piuttosto figure operative esperte a cui rivolgersi più per un parere tecnico che per ricevere indicazioni su cosa fare o sulle priorità d’intervento.
L’azienda inoltre, per scelta, aveva deciso di non disporre di un piano di manutenzione aziendale programmata a medio/lungo termine e aveva deciso di ridurre – al fine di ottenere un risparmio di costi – gli interventi di routine per le piccole manutenzioni periodiche. È facile però immaginare che al sopraggiungere di un guasto o di una rottura, i tempi di reazione diventavano più lunghi del previsto poiché, seppure il manutentore verificava l’entità del guasto, l’intervento di ripristino non poteva essere così immediato e risolutivo, specie in mancanza dei pezzi di ricambio.
Altro elemento limitante era la mancanza di un budget dedicato per interventi di impatto economico contenuto che venivano così inseriti in un iter di approvazione lungo e sproporzionato.
Per quanto riguarda il personale operativo ognuno aveva delle competenze specifiche ben definite; non erano stati definiti piani di formazione per accrescere le competenze dei vari manutentori né momenti formali di scambio delle esperienze e di condivisione dei problemi. Quindi all’arrivo di nuove risorse, la loro formazione non era né strutturata né pianificata. Inoltre, non era previsto un controllo delle attività dei manutentori: mancava una raccolta dati relativi agli interventi (sia in programma che effettuati) e mancava un’analisi dell’efficacia degli interventi effettuati: spesso questi erano svolti più volte sulle stesse macchine perché nel tempo le soluzioni individuate non risultavano efficaci.
Infine, non esistevano KPI per misurare le performance del processo di manutenzione , compresi quelli di valutazione dei costi di intervento.
È evidente che i punti critici individuati denotavano una situazione di non-governo della funzione, sia a livello di attività operative che come visione strategica delle manutenzioni in ottica di miglioramento aziendale.
Dopo aver condiviso le criticità riscontrate e aver preso coscienza delle problematiche annesse è stato possibile iniziare a ragionare su un concreto percorso di miglioramento.
Il primo passo è stato quello di lavorare sul controllo delle attività introducendo un file per la registrazione di tutte le attività di manutenzione dei sistemi produttivi al fine di raccogliere informazioni sulla tipologia di intervento effettuato, sulla loro programmazione, sull’urgenza delle chiamate provenienti dai reparti e sull’efficacia delle azioni intraprese e dei costi connessi.
Unitamente al registro è stato immediatamente introdotto un modulo per mettere sotto controllo le richieste di intervento con lo scopo di avere visibilità del numero di chiamate e degli interventi che venivano effettivamente svolti ogni giorno. Di conseguenza, diventava possibile tracciare l’operatore che aveva effettuato l’intervento, oltre che la durata e l’efficacia dello stesso. La responsabilità della corretta compilazione del modulo è stata assegnata ai singoli reparti che così fungevano da controllori.
Infine, è stato chiesto ai singoli manutentori delle macchine di redigere un rapporto giornaliero del lavoro svolto con l’obiettivo di valutare la loro produttività e le cause primarie degli interventi fatti.
Tutte le informazioni raccolte hanno permesso di creare da subito un data base unico di informazioni utilizzabili per creare gli indicatori aziendali fondamentali per il controllo del processo di manutenzione.
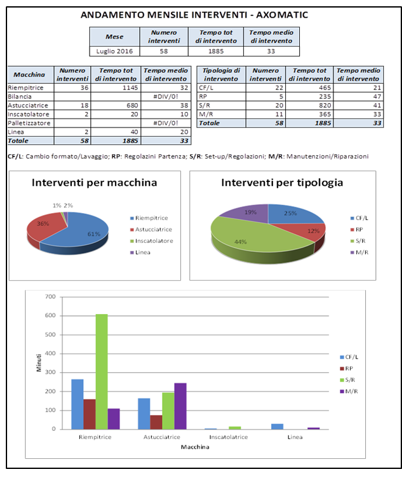
Per quanto riguarda il personale operativo la scelta è stata quella di istituire un gruppo di miglioramento, denominato “Kaizen Team” che, con frequenza settimanale, ha iniziato a incontrarsi per discutere le problematiche riscontrate, per confrontarsi su specifici interventi effettuati, per ragionare su possibili azioni di miglioramento e per rivalidare il programma degli interventi delle settimane successive.
Con queste prime azioni è stato dunque possibile passare da una situazione difficile, al limite della governabilità, ad una dove il processo di gestione della manutenzione era finalmente sotto controllo e misurabile.
Indipendentemente dall’approccio utilizzato, anche il processo di manutenzione deve poter dare il suo contributo al miglioramento dell'Operations Management attraverso il controllo delle attività, della loro tempestività e della loro efficacia, non dimenticando le nuove tecnologie – come ad esempio la realtà aumentata – che su questa funzione avranno un impatto sempre più rilevante.
Riproduzione riservata©