La corretta gestione delle Operations nelle PMI è un aspetto chiave per rimanere competitivi sui mercati e per garantire un elevato livello di servizio in termini di flessibilità e puntualità nelle consegne. In questo articolo, attraverso un caso pratico, vogliamo raccontare un approccio integrato sulle Operations che ha coinvolto tutta l'azienda.
CONTESTO
LEMA è un’azienda commerciale operante nel settore Automotive, leader a livello nazionale e internazionale per la ricambistica di veicoli industriali, che offre una vasta gamma di prodotti in costante aggiornamento con l’introduzione di nuovi modelli.
Nel 1996 LEMA sente l’esigenza di attivare una propria linea produttiva e per questo rileva un fornitore strategico. Da questa fusione nasce ARIS, azienda che affianca alla produzione automotive anche un’attività piuttosto importante nel mercato delle membrane.
Il mercato che ARIS vuole servire richiede:
- puntualità nelle consegne
- qualità estremamente elevata dei prodotti
- alto livello di flessibilità produttiva
Tutto questo comporta per l’azienda un salto di qualità a livello produttivo, e la necessità di industrializzare i processi e riorganizzarsi in modo più efficiente. Inoltre, la direzione del reparto produttivo aveva visto fino a quel momento un avvicendamento frequente di diversi responsabili, cosa che non aveva agevolato lo sviluppo di una metodologia lavorativa costante nel tempo.
Un vasto parco macchine (fustellatrici, plotter, presse e macchine per la serigrafia) assicura ad ARIS molteplici produzioni: campionature, prototipazioni e ovviamente produzioni di serie. Tuttavia, nonostante le dimensioni ridotte che avrebbero dovuto garantirle una notevole elasticità, l’azienda non aveva ancora trovato la chiave corretta per sfruttare tutte le proprie potenzialità.
OPTA, dopo avere effettuato un check preliminare ma completo sullo "stato attuale" aziendale ha proposto alla Direzione Generale un piano di intervento focalizzato su alcuni punti specifici:
- messa sotto controllo del portafoglio ordinato e spedito in modo da rendere l'azienda più flessibile alle esigenze di mercato
- messa sotto controllo dei costi della manodopera per aumentare la marginalità
- crescita professionale del personale (sia diretto che indiretto) su aspetti tecnici, metodologici e di management, oltre al rafforzamento della figura del capo reparto.
Cabina di regia
Per rispondere al primo obiettivo è stata costituita una cabina di regia nella quale erano coinvolti sia i consulenti OPTA che la proprietà aziendale, con l’obiettivo di aggiornare il management sulle evoluzioni dell’azienda, condividere i dati del portafoglio, dell’ordinato, dello spedito e il controllo dei ritardi.
La situazione di partenza vedeva questo quadro:
- ordini in ritardo (16% del portafoglio mensile)
- scarsa visibilità degli ordini entrati e, quindi, del carico lavoro
- pianificazione non focalizzata sul rispetto delle date di consegna confermate ai clienti.
Per agevolare il monitoraggio è stato introdotto un tool che chiameremo “Monitor Direzionale Operations”, con l'obiettivo di misurare i dati relativi all’acquisizione ordini clienti, al portafoglio ordini e al fatturato.
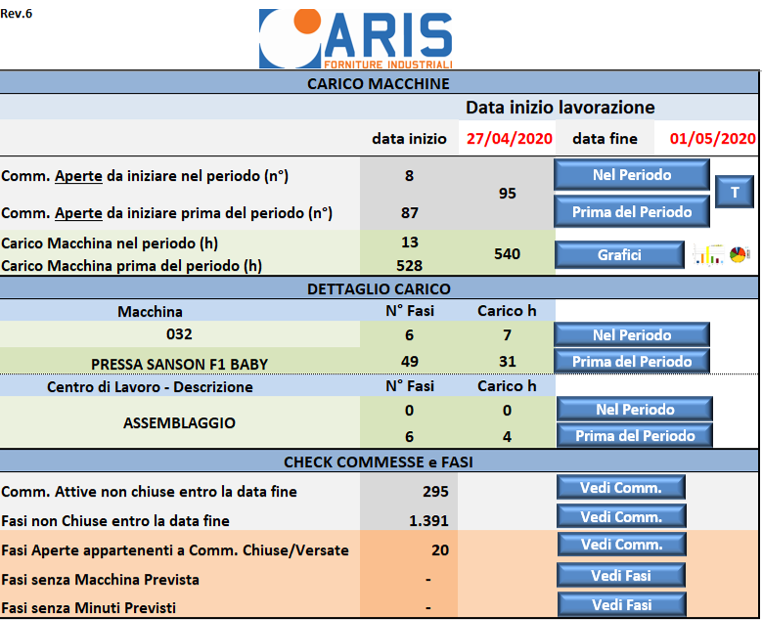
Dai primi numeri raccolti, è emersa la necessità di agire sui principali processi di Operations: la Produzione e il Planning. Lo scopo era aumentare l’efficienza produttiva ovvero liberare capacità a vantaggio di una maggiore flessibilità.
Nell'ambito degli interventi sul processo produttivo, sono state decise una serie di azioni di seguito descritte:
- focalizzare il tempo del capo reparto principalmente sul controllo dell’avanzamento della produzione, sull'organizzazione del lavoro, sull'ottimizzazione nell’utilizzo delle materie prime e sulla gestione del carico lavoro delle macchine. Per recuperare i ritardi e/o avvisare i clienti in tempo utile su eventuali problemi il focus è stato posto sul rispetto tassativo degli ordini da evadere e sulla disponibilità delle attrezzature necessarie alla produzione con un orizzonte avanti di due mesi.
- snellire i metodi di lavoro e introdurre attrezzature che potessero ridurre i tempi produttivi e le attività di fermo macchina aumentando così l'efficienza produttiva.
- mettere sotto controllo il carico di lavoro (operatori, macchine e reparti) per evitare fermi o rallentamenti produttivi dovuti a scarsa visibilità sulle commesse. Per favorire questo processo è stato introdotto un tool ad hoc che abbiamo chiamato “Monitor Commesse”.
- revisionare e aggiornare i cicli produttivi per fornire agli operatori tempi di riferimento attendibili e corretti e, allo stesso tempo, rendere più affidabile il carico di lavoro (sia nel mese in corso, ma soprattutto per i tre mesi successivi). Ovviamente non era possibile revisionare e aggiornare tutti i cicli in poco tempo; per questo l'intervento è stato focalizzato laddove veniva riscontrato un elevato scostamento tra il tempo previsto e quello effettivamente dichiarato in produzione. L’allineamento dei tempi (previsti vs effettivi) e l'introduzione di un terzo tool dedicato a misurare l'efficienza (“Monitor Efficienza”) ha consentito un miglior controllo sul processo stimolando positivamente le persone verso il miglioramento.
Dall'analisi dell’efficienza è emerso che il tempo di attrezzaggio (benestare) era un elemento alquanto critico in quanto ARIS si trova a dover produrre piccoli lotti (prototipazioni) che non sempre possono essere fatti a plotter. Per questo motivo, era necessario revisionare il layout aziendale per poter agevolare il benestare e ridurre quindi i tempi di attesa macchina.
In particolare, nel reparto fustellatura era presente un macchinario che, rispetto agli altri disponibili, permette la realizzazione di articoli di dimensioni maggiori garantendo una buona flessibilità produttiva. Le performance di questa fustellatrice erano però mortificate da tempi di piazzamento molto lunghi. Abbiamo rilevato che la macchina si trovava in corrispondenza di un pilastro che limitava lo spazio di lavoro e obbligava ad un continuo spostamento del portarotolo. Abbiamo così deciso di spostare il macchinario in un luogo più idoneo e spazioso arrivando ad una diminuzione del tempo di attrezzaggio del 30%. La stessa macchina era inoltre utilizzata in maniera molto sporadica; il personale interno non aveva ancora capito come sfruttarla a dovere. Alcune azioni mirate, volte a risolvere problematiche produttive concrete, hanno sbloccato la situazione e portato ad un aumento della produttività su quella macchina dell’80%, scaricando altri macchinari addirittura del 300% per effetto del miglioramento di efficienza.
Per poter aumentare la disponibilità dei macchinari anche nel reparto tranciatura, abbiamo deciso di intervenire sulla disposizione delle materie prime, riorganizzando la disposizione dei materiali tramite una gestione a vista e secondo la logica ABC in modo da monitorare la giacenza dei materiali ed evitare rotture di stock, oltre a permettere un prelievo efficiente (i tempi di picking si sono ridotti del 30%).
Le azioni descritte hanno permesso un efficientamento complessivo del processo produttivo del 22%, nell’arco di 10 mesi mentre l’OEE macchina è passato dal 55% al 78%.
Inoltre, per poter garantire marginalità all’azienda è stato ottenuto un notevole miglioramento nell’utilizzo della Manodopera Diretta (OEE MOD), che è cresciuto dal 78% all’87%.
Per quanto riguarda il Planning, abbiamo modificato le logiche di pianificazione sia all'interno dell'ERP che direttamente sul campo introducendo modalità di gestione a vista degli ordini di produzione favorendo in questo modo la produzione e, in particolare, gli attrezzaggi.
Insieme al capo reparto, siamo riusciti nel giro di pochi mesi a recuperare il ritardo che si era generato e a produrre con un anticipo di un mese. L'aver messo sotto controllo l’avanzamento della produzione ha permesso di abbattere i ritardi consegna dal 16% al 4%.
Un'altra azione, all'apparenza scontata, che ha dato significativi risultati in termini di riduzione dei fermi produttivi, è stata quella di sottoporre le attrezzature ad un controllo qualitativo preventivo,
Dal punto di vista della misurazione è stato introdotto l’indicatore sul livello di servizio al cliente (On Time Delivery – OTD). Grazie ad un’accurata gestione delle date di consegna confermate al cliente, è stato possibile migliorare sensibilmente il Livello di Servizio stabilizzando l’indicatore OTD al 95%. Il monitoraggio continuo dell’avanzamento delle commesse ci permette ora, in caso di difficoltà, di informare con un mese di anticipo i clienti di eventuali ritardi e di concordare una nuova data di consegna.
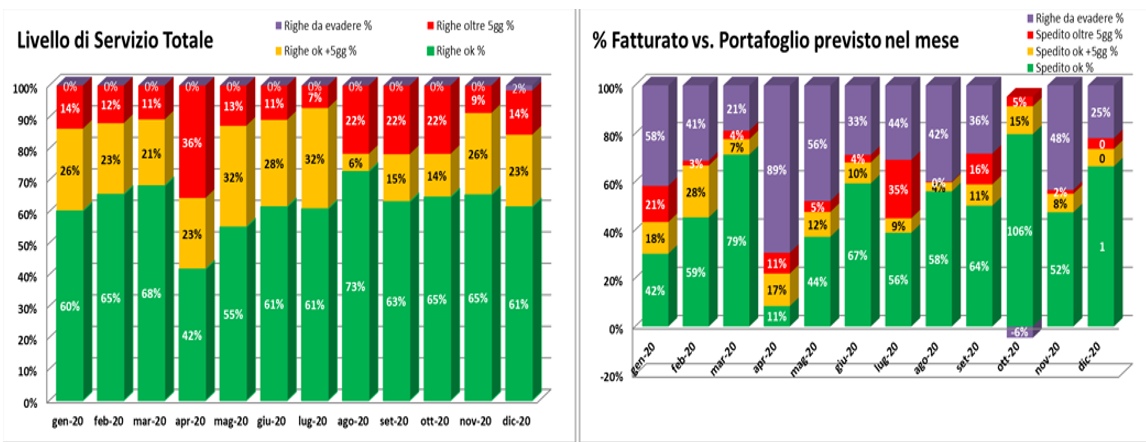
Tutte le azioni messe in campo che hanno impattato sull'organizzazione del lavoro e sugli strumenti hanno prodotto un effetto boomerang che ha coinvolto tutto il personale a 360 gradi. Metodologie lavorative inconsuete sono state sperimentate con eccellenti risultati, sia in termini di miglioramento della qualità di lavoro ma, soprattutto, di riduzione dei tempi di produzione.
La maggior consapevolezza acquisita dall'azienda ha permesso, inoltre, di far emergere diverse considerazioni sugli aspetti più disparati:
- analisi del rapporto fra manodopera diretta/manodopera indiretta/pezzi prodotti in ottica di revisione delle politiche di costificazione
- recupero interno di attività affidate a Terzisti
- revisione generale dei costi degli articoli con riposizionamento sul mercato
Ancora oggi stanno emergendo nuovi stimoli sia per quanto riguarda gli approvvigionamenti ma anche e soprattutto per attività di tipo commerciale con lo sviluppo di nuovi sistemi di analisi su clienti, agenti e fatturato (con focus sulle singole regioni), così da concentrare le risorse su azioni mirate e ben calibrate di incremento delle vendite, sia verso clienti acquisiti che verso la ricerca di nuovi canali di vendita.
Uno degli aspetti più importanti che ha permesso un risultato così brillante è stata la creazione di un team interno di lavoro in cui si sono perfettamente amalgamati consulenti, capo reparto e proprietà. La consulenza tecnica è diventata il promotore di una ristrutturazione “mentale” che si è appoggiata sulle migliori fondamenta: le persone.
Riproduzione riservata©