Negli ultimi anni le aziende hanno trovato nel “back to basics” dell’industrial engineering nuove opportunità di crescita o di razionalizzazione. Tra questi fondamentali, un esempio è rappresentato dai Tempi & Metodi.
In questo articolo vedremo come Cocif (leader italiano nella produzione di porte e finestre), nell’ambito di un progetto più generale di allineamento della propria supply chain alle richieste del mercato, sia ricorso alla metodologia Tempi e Metodi (se sei interessato ad approfondire come sia stato condotto il progetto leggi l’articolo “Cocif: un percorso di successo per il miglioramento delle operations ”).
L’azienda aveva necessità di attualizzare e di stabilizzare in numeri le molte esperienze e la conoscenza dei singoli, passando da un sapere esperienziale (utile per capire il livello di sensibilità presente in azienda) a dati sistemici.
La campagna di raccolta tempi, avvenuta reparto per reparto, ha portato non solo a ottenere tempi più affidabili e veritieri ma è stato il primo passo per un ammodernamento dal punto di vista dei metodi di lavoro, della corretta suddivisione delle attività e, infine, del recupero di produttività.
Il percorso ipotizzato non era affatto banale in quanto gli ambiti di applicazione dell’analisi presentavano caratteristiche molto diverse tra loro (da impianti complessi a lavorazioni manuali). È stato, pertanto, necessario suddividerlo nelle due componenti principali dell’infisso: l’anta e lo stipite.
In tal modo, si è partiti dalle fasi di produzione degli infissi, per poi proseguire lungo il flusso delle lavorazioni: dal taglio del legno, alle lavorazioni di profilatura e verniciatura, fino al montaggio e imballo del prodotto finito.
Di particolare interesse è stata la relazione con il personale operativo; infatti, attraverso le loro conoscenze e i loro modi di operare, abbiamo compreso quale fosse il modo più corretto di registrare il lavoro al fine di ottenere dati numerici confrontabili che rappresentassero le reali modalità di lavoro.
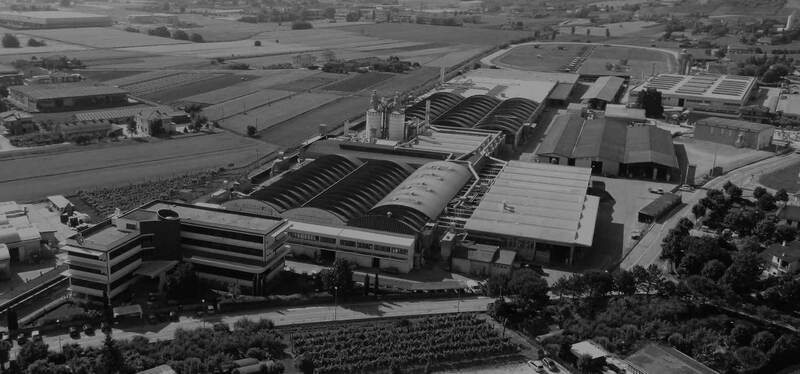
Altrettanto importante è stata l’interazione con l’ingegneria di processo, con la quale abbiamo collaborato per affinare i modelli già esistenti. L’obiettivo era di riuscire a identificare le attività elementari, così da ottenere una corrispondenza precisa con le tempistiche contemplate nel configuratore prodotto.
Nel caso di Cocif gli infissi rappresentano un componente realizzato su misura; questa caratteristica ci impone di interrogarci su un quesito specifico: come possiamo determinare i tempi standard su prodotti così diversi uno dall’altro?
La risposta è semplice: il rilievo dei tempi non deve avere come focus il prodotto, ma la singola lavorazione. Definito ciò, occorre determinare le logiche di funzionalità degli impianti e delle lavorazioni per ogni modello di infisso.
La parte più complessa della campagna Tempi e Metodi non è stata perciò quella dei rilievi, ma piuttosto quella della comprensione dei parametri che caratterizzavano il lavoro, così da attribuire un corretto tempo/peso.
A livello tecnico questo lavoro è risultato estremamente utile anche per tutte le persone coinvolte nel progetto; infatti, è stato possibile capire:
- cosa realmente incide sulla corretta conduzione macchina e sulla corretta esecuzione della lavorazione;
- che eseguire il lavoro con una sequenza di attività piuttosto che un’altra ha una incidenza diretta sul rendimento dell’impianto e della postazione di lavoro.
Come sempre l’analisi Tempi e Metodi è time consuming: in questo caso oltre alla numerosità delle lavorazioni da considerare (circa 40 in totale) c’è stata anche l’attività importante di parametrizzazione del dato. Lo scopo era determinare e tempificare i parametri per ogni fase del ciclo di lavorazione dell’infisso, con l’intento finale di attribuire un tempo a ogni oggetto configurato, riuscendo a intercettare tutte le possibili casistiche previste a listino e/o richieste dal cliente.
Tuttavia, lo sforzo dell’applicazione dei tempi parametrici ha consentito il raggiungimento di diversi obiettivi e i vantaggi; tra i principali:
- ottenere una giusta costificazione di prodotto;
- definire i tempi ciclo di prodotto;
- determinare l’impiego degli impianti/aree di lavoro;
- verificare l’efficienza produttiva in real time (grazie al MES);
- supportare il miglioramento continuo della produzione.
Quali i risultati ottenuti:
- revisione dei tempi di produzione, sia relativi agli impianti automatici (miglioramento di circa il 3%-5%) che alle attività manuali (25%-30%);
- miglioramenti legati alle modalità di lavoro ed al numero di operatori utilizzati, al layout, al bilanciamento delle fasi di lavoro.
L’impiego dei Tempi e Metodi si è rivelato dunque molto importante per far emergere dinamiche di inefficienza e consentire all’azienda di agire di conseguenza.
Il prossimo passo sarà quello di verificare, una volta caricati i tempi parametrici sul configuratore, l’effettiva aderenza alle produzioni, sia quelle standard che quelle più customizzate.
Riproduzione riservata©