È possibile parlare di tempi e metodi anche nella logistica aziendale?
Sicuramente sì, anche per le crescenti esigenze di misurazione della produttività ed efficienza legate al settore.
Non è solo un problema di livello di servizio, ma anche di capacità di rispondere alle richieste dei clienti attraverso una struttura reattiva e organizzata che, a sua volta, sappia massimizzare il risultato. Ecco allora che la logistica inizia a sfruttare tecniche e logiche che, fino a poco tempo fa, erano esclusivo appannaggio delle realtà produttive.
Non stupisce quindi come anche la metodologia dei tempi e metodi possa essere utilizzata anche in ambito logistico, specie quando, a contorno delle attività di ingresso e uscita merci, ci sono attività di trasformazione come piccole lavorazioni, smistamento, imballaggio ecc.
Il caso che vogliamo illustrarvi è quello di una azienda del settore moda che ha richiesto un’analisi di dettaglio per valutare l’efficienza del flusso principale di smistamento dei propri prodotti.
I volumi giornalieri del magazzino erano di circa 14.000 colli in ingresso per 150.000 kit smistati in uscita. Ogni giorno lavoravano in questo hub circa 350 operatori tra addetti alle movimentazioni, imballaggio e preparazione delle spedizioni.
Quali tecniche e strumenti utilizzare per analizzare un flusso in una realtà complessa dall’arrivo della merce dai fornitori fino alla spedizione ai singoli punti vendita?
Le tipologie di rilievo adottate sono state varie, poiché varie sono le caratteristiche delle attività del magazzino. Da una parte si utilizzano macchine per la gestione del materiale in ingresso e lo smistamento dei singoli kit, dall’altra si effettuano attività tipicamente logistiche come le movimentazioni, lo stoccaggio, il picking, la ventilazione nelle baie di accumulo e la preparazione delle spedizioni.
Le tecniche tempi e metodi utilizzate sono state:
- rilievo cronotecnico per le attività di produzione;
- work sampling per le attività a contorno (movimentazione, prelievi, asservimento sorter).
Sono stati realizzati più di 6.000 rilievi su oltre 700 pallet, 5.500 colli, 70.000 kit e girate più di 20 ore di filmati.
Per rispondere all’obiettivo di misurare la produttività delle singole fasi del processo, abbiamo fatto ricorso non solo ai tempi e metodi, ma anche alle logiche della Lean Production per riuscire a classificare le attività secondo il principio di valore aggiunto e di spreco.
Per ogni singola fase di lavoro sono state individuate le attività elementari; da qui, attraverso filmati e/o campionamenti sul campo, sono stati individuati i tempi di riferimento. Alle attività cicliche (che si ripetono ogni volta su singolo kit) si sono aggiunte:
- le attività periodiche, ovvero attività a ciclo ma che si ripetono a cadenze diverse (ad esempio controlli qualità a campione, movimentazione bancali);
- le attività accidentali che sono attività non previste e non attese (ad esempio rotture, fermi impianto, duplicazione di attività già svolte).
Tutte le attività considerate (cicliche, periodiche e accidentali) sono state ulteriormente classificate come:
- attività a valore aggiunto: tutte quelle attività che trasformano l’oggetto da uno stato a un altro;
- attività a non valore aggiunto: attività che non incidono sullo stato dell’oggetto ma che vengono svolte poiché considerate utili nel flusso delle operazioni;
- sprechi: tutto ciò che rappresenta una attività superflua e che non ha incidenza sul flusso delle operazioni e sul prodotto.
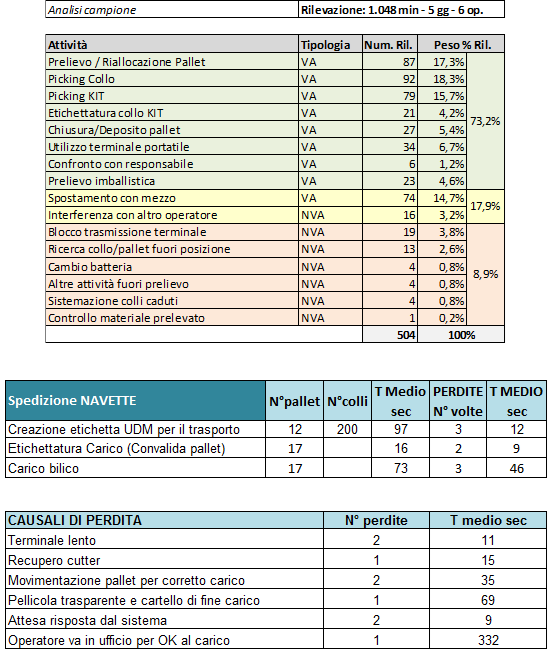
Dalla raccolta dati e dall’individuazione delle attività a non valore aggiunto è scaturita un’attività di individuazione di azioni di miglioramento.
Tornando al lavoro di determinazione dei tempi di riferimento, alcuni aspetti critici hanno riguardato le seguenti attività:
- rendere significativi i campionamenti per singola fase;
- svincolare i rilievi dagli effetti legati alla stagionalità (numerosità di colli/kit);
- individuare una metodologia di lavoro che potesse definirsi “di riferimento”.
Il confronto con i referenti aziendali e l’analisi dei dati storici su un periodo annuale, hanno permesso di individuare il giusto campionamento per le diverse fasi del processo logistico/produttivo.
La rappresentazione delle attività per movimenti elementari ha permesso, inoltre, di distinguere le fasi “fisse”, cioè quelle ripetitive e non influenzate dalla variabilità dei volumi, da quelle “variabili” ossia legate alla numerosità dei colli/kit.
Infine, il coinvolgimento di un ampio numero di persone durante i rilievi ha aiutato l’individuazione sia delle attività “di riferimento” sia dei relativi tempi, evitando di focalizzarsi su performance particolarmente positive o negative per metodo e per velocità di esecuzione.
I dati suddivisi in attività elementari sono stati poi riconciliati e aggregati in maniera da rispettare la suddivisione delle fasi che l’azienda utilizza nella gestione e assegnare, per singola voce aggregata, un valore di efficienza tra le tempistiche ottimizzate (cioè senza perdite) e quelle rilevate (comprese le perdite).
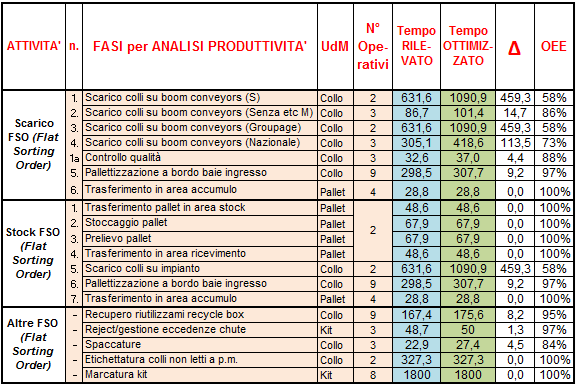
A questo punto è stato aggiunto un ulteriore elemento all’analisi di produttività ed efficienza: il dimensionamento delle risorse necessarie al processo logistico/produttivo.
Per ogni macroprocesso sono stati considerati:
- i tempi rilevati ottimizzati;
- le perdite rilevate;
- il coefficiente di affaticamento calcolato secondo valori standard tabellati;
- le eventuali criticità date dall’organizzazione.
I tempi sono stati trasformati in FTE (Full Time Equivalent) ed è stato calcolato il numero degli:
- operatori teorici (senza alcuna perdita accettata);
- operatori calcolati (con le perdite rilevate e coefficiente di affaticamento);
- operatori rilevati (risorse effettivamente presenti in magazzino al momento dei rilievi sul campo).
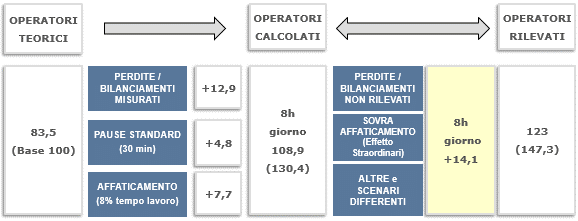
Risultati ottenuti:
- definizione delle tempistiche di riferimento per singola attività svolta in magazzino;
- individuazione delle principali causali di inefficienza;
- confrontabilità dei driver aziendali rispetto alle tempistiche individuate;
- dimensionamento delle risorse uomo FTE necessarie.
I tempi e metodi anche in questo progetto di logistica aziendale hanno dimostrato di essere un efficace strumento per mettere sotto controllo un sistema logistico/produttivo.
Attraverso la determinazione dei tempi e lo studio delle metodologie di lavoro è possibile valutare la produttività delle persone e del sistema, esplicitare l’efficienza dell’organizzazione, razionalizzare i flussi delle attività, bilanciare le fasi di lavoro, evidenziare gli sprechi e individuare opportune azioni di miglioramento.
Riproduzione riservata©