La logistica produttiva è spesso suddivisa nei suoi ruoli, mansioni e processi tra i vari reparti e, al tempo stesso, è scollegata dalle altre aree della logistica interna (logistica distributiva e logistica di magazzino) se presente come reparto a sé stante che si occupa principalmente del ricevimento, dello stoccaggio e della spedizione dei prodotti finiti al cliente finale.
Non esiste quindi un vero “ente” logistico in grado di governare tutti i flussi di materiale, siano essi di asservimento alle linee di produzione che di consegna al cliente finale.
Per quanto riguarda la logistica interna, il confine tra la logistica di produzione e la logistica di magazzino può essere molto labile, confuso e, di conseguenza, portatore di inefficienza. Non a caso è abbastanza frequente riscontrare che molte attività proprie della logistica produttiva e della logistica di magazzino vengano effettuate da personale diretto di produzione.
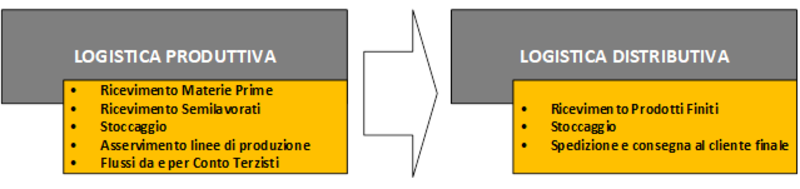
Provate ad immaginare la movimentazione interna dei componenti e dei prodotti affidata ai capisquadra e ai capireparto della vostra azienda. Il risultato sarebbe quello di impegnare le vostre risorse produttive in attività di ricerca e movimentazione dei componenti da asservire ai reparti a scapito delle attività di coordinamento e di produzione. In termini Lean la movimentazione e la ricerca dei materiali sono due dei sette sprechi “capitali” quindi il problema non è tanto l’efficacia, ma piuttosto l’efficienza, specie al crescere dei volumi da movimentare.
Venendo al caso specifico, vogliamo illustrarvi il caso della Casta srl, che ha sede nel Salento e opera nel settore della carpenteria medio-leggera fornendo componenti di alta qualità per la produzione di carrelli elevatori e macchine agricole di grandi gruppi multinazionali.
La produzione dell’azienda riguarda un’ampia gamma di prodotti (telai, forche, piattaforme, porta batterie, serbatoi, etc.) che spaziano per tipologia, dimensioni, peso, lavorazione e finitura. I prodotti vengono realizzati partendo dalla materia prima (lamiere e tubi) e passando attraverso lavorazioni di taglio laser, piegatura, sabbiatura, saldatura e, sovente, di verniciatura.
Dopo aver intrapreso con successo un progetto di efficientamento delle linee di saldatura, l’azienda ha rivolto il proprio sguardo al sistema logistico interno individuando due aree di criticità e di possibile intervento:
- governo ed efficienza dei flussi logistici
- automatizzazione dei processi di emissione dei documenti a supporto delle attività di magazzino (BEM, DDT, Liste di prelievo, etc.).
Le principali attività “non a valore” riguardanti i flussi dei materiali riscontrate nella fase preliminare di analisi hanno riguardato:
- ricerca dei materiali
- gestione degli spazi
- identificazione dei materiali
- prodotti mancanti
- differenze inventariali
- attese
Per quanto concerne la gestione documentale si è evidenziata una forte componente manuale nell’emissione e/o elaborazione dei documenti oltre all’assenza di alcuni strumenti informativi.
L’Azienda ha quindi deciso di intraprendere un progetto di completa revisione organizzativa con l’obiettivo di creare un “ente logistico” in grado di governare in maniera efficiente tutti i flussi di movimentazione dei materiali a prescindere dal cliente, interno o esterno.
La situazione iniziale si presentava come segue:
- con il termine logistica interna veniva identificata la sola pianificazione della produzione
- con il termine magazzino venivano identificate le attività connesse ai processi inbound, di stoccaggio (semilavorati in ingresso da fornitori e prodotti finiti) e di spedizione al cliente finale
- il personale diretto svolgeva attività indirette di magazzino (stoccaggio semilavorati provenienti da altri centri di lavoro interni, prelievo semilavorati e asservimento linee)
- l’organizzazione era di fatto una autogestione non strutturata, manuale ed affidata alla diligenza ed esperienza del personale.
Era quindi necessario fare chiarezza sugli obiettivi, sui ruoli chiave (ad es.: Responsabile logistica, Addetto di magazzino, Service man, etc.) e sulle mansioni.
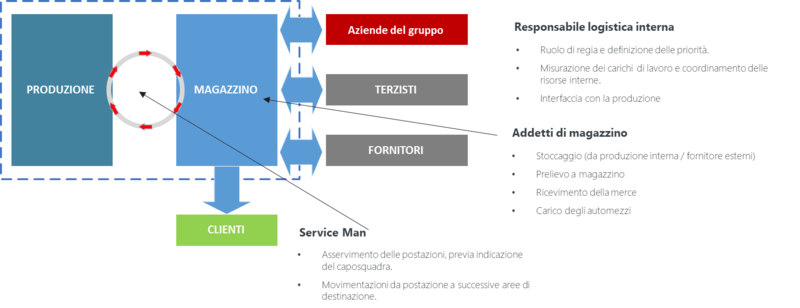
Successivamente occorreva:
- mappare in dettaglio i flussi fisici ed informativi al fine di determinare l’entità dei flussi principali, le priorità di intervento, le aree di competenza e le specifiche per la modifica e/o l’implementazione degli strumenti informativi;
- riorganizzare il magazzino semilavorati in termini di layout e aree di interscambio;
- mappare le aree di stoccaggio al fine di garantire una efficace ed efficiente rintracciabilità dei prodotti
- sviluppare gli strumenti informativi di supporto come la gestione della mappa di magazzino, le etichette di identificazione del prodotto con esplicitata la destinazione (fase di lavoro successiva, terzista, cliente, etc.), le liste di prelievo e la Bem;
- formare il personale addetto alla logistica e alla produzione riguardo agli obiettivi del progetto, alle logiche base di funzionamento del nuovo sistema logistico e, infine, alle modalità di utilizzo degli strumenti informatici implementati
- implementare gradualmente le soluzioni adottate monitorando costantemente i risultati e intervenendo prontamente sulle criticità che via via si evidenziavano.
Dopo circa un mese dall’avvio, raggiunta la stabilità e la standardizzazione del processo, il progetto è andato avanti con un progressivo fine tuning durante il quale sono state apportate migliorie agli strumenti informativi di supporto al processo. È stato poi deciso di estendere il progetto con l’obiettivo di arrivare a coprire tutti i reparti produttivi nel giro di qualche mese.
I principali risultati conseguiti possono essere così sintetizzati:
- incremento ulteriore dell’OEE delle linee di saldatura;
- incremento della produttività nel processo di prelievo grazie alla riduzione dei tempi ricerca del materiale;
- incremento della produttività nel processo di stoccaggio grazie alla mappatura ed all’indicazione della destinazione nell’identificativo prodotto;
- riduzione delle attese per la preparazione dei kit di produzione;
- riduzione delle attese e/o delle inefficienze dovute al prelievo di kit con articoli mancanti (gli articoli mancanti vengono “tirati” in anticipo rispetto alla situazione pregressa).
I risultati ottenuti in Casta e in altri progetti analoghi di integrazione evidenziano l’importanza e la necessità di approcciare la logistica aziendale e, in particolar modo, la logistica produttiva attraverso una visione unitaria e di sistema quale ulteriore leva strategica per il raggiungimento degli obiettivi aziendali di efficienza e di miglioramento del livello di servizio al cliente finale.
Riproduzione riservata©