Uno dei punti critici nell'ambito dei sistemi di pianificazione della produzione è quello relativo alla gestione dei mancanti. Il processo di pianificazione prevede infatti l’assegnazione di compiti alle diverse risorse, interne ed esterne all’azienda, per far sì che il prodotto sia disponibile in un luogo stabilito e nel momento richiesto. L’attività di pianificazione rischia però di non avere piena efficacia se non vengono effettuate, con il dovuto anticipo, opportune verifiche sulla fattibilità di quanto programmato.
Una delle principali verifiche da compiere riguarda la disponibilità di materie prime, semilavorati e componenti necessari alla produzione. Spesso, infatti, per problemi contingenti, non tutto quello che si è pianificato è disponibile nei tempi previsti. In tal caso si generano dei mancanti in produzione.
Ma non è detto che il materiale manchi solo a causa di ritardi del fornitore: spesso tutta l’azienda concorre alla generazione di mancanti. Per esempio a causa di fermi macchina per la mancanza di un adeguato piano di manutenzione, per distinte errate, per carenze nei contratti con fornitori, per assenza o poca definizione del livello di servizio al cliente, per una politica delle scorte poco efficiente, ecc.
Vale la pena citare un esempio interessante di impostazione di una gestione corretta dei mancanti. Parliamo della Italcab Spa, azienda veneta che produce cabine per mezzi per movimento terra ed affini che, con il supporto di OPTA, ha affrontato il tema che qui trattiamo.
Il lungo processo produttivo di Italcab prevede diverse lavorazioni interne, l’acquisto di molti componenti ed un assemblaggio finale che porta la cabina allo stato finito. Tra i motivi di ritardo nelle consegne, uno dei principali era stato identificato nella presenza di mancanti per l’assemblaggio finale. L'azienda ha formato un team di lavoro che prevedeva il coinvolgimento del Responsabile Logistica (Marco Cazzaro) e del Responsabile Magazzino (Simone Cardin) con l'obiettivo di risolvere il problema operando su diversi fronti.
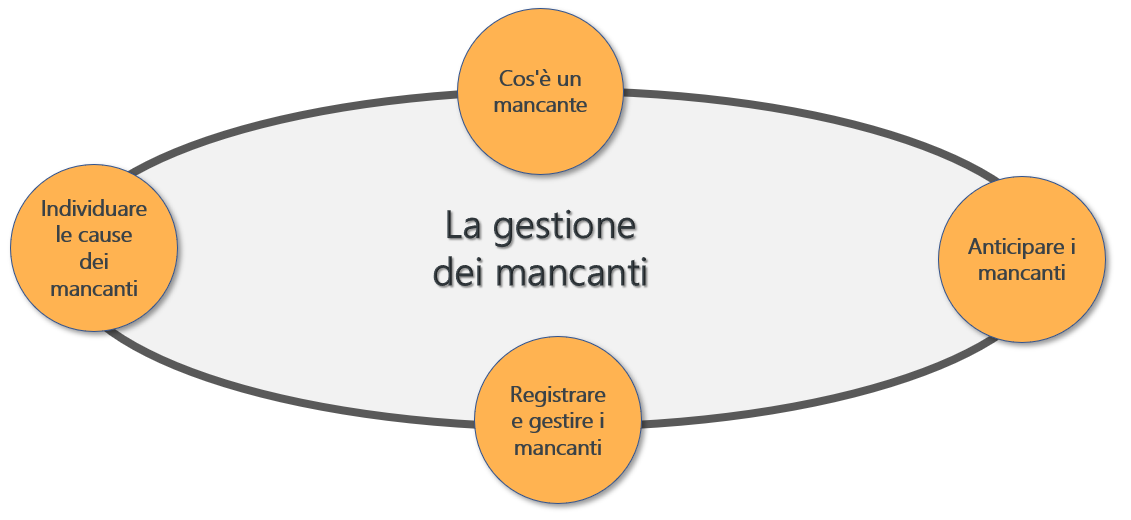
Si è proceduto attraverso questi 4 step:
- Definizione del concetto di mancante e conseguente misura corretta del fenomeno. In azienda era presente una certa confusione sul concetto di mancante. Ci possono essere infatti mancanti al prelievo dal magazzino, all’assemblaggio o per il venduto e non tutti hanno la stessa importanza. In una prima fase è stato deciso di focalizzarsi sui mancanti per il venduto.
- Previsione, con un minimo in anticipo, dei mancanti per gli assemblaggi necessari per le vendite a breve termine. È stato progettato un apposito tool nel software gestionale che analizza il piano di montaggio necessario a coprire la domanda generata dal portafoglio ordini con orizzonte temporale a una settimana.
Attraverso l'esplosione dei fabbisogni dei componenti avviene il confronto con la disponibilità degli stessi. Una stampa generata al termine dell’analisi propone un elenco dei componenti destinati a mancare in fase di assemblaggio e diventa uno strumento di lavoro per la riunione settimanale di pianificazione. In quest’ultima si pattuiscono le eventuali modifiche da effettuare al piano di assemblaggio e le attività di sollecito da fare verso i fornitori e verso i reparti di lavorazioni interne.
- Registrazione e gestione dei mancanti. È stato creato un database in cui registrare sia i mancanti emersi dalla stampa (vedi punto precedente), sia quelli emersi durante le fasi lavorative che dipendono tipicamente da errori inventariali o da Non Conformità individuate in fase di assemblaggio.
La registrazione permette di condividere, con tutti gli enti interessati, le informazioni utili a tutto il processo di gestione dell’urgenza: dal sollecito al fornitore fino alla consegna al reparto di destinazione. Le informazioni minime condivise sono: codice articolo, fornitore, reparto di destinazione, quantità mancante, data di fabbisogno e data di previsto arrivo. La gestione tramite un database centralizzato riduce notevolmente lo scambio di informazioni via e-mail e telefono, tipicamente incomplete e molto dispendiose in termini di tempo.
- Conteggio dei mancanti ed individuazione delle cause. Registrare i mancanti permette, oltre che innescare le attività di gestione immediata, di lavorare sulle motivazioni che generano gli stessi allo scopo di ridurne le casistiche. Dalla stampa si ricava un conteggio settimanale che nel tempo permette di valutare l’andamento degli stessi mancanti ed intercettare eventuali derive negative.
Altro aspetto importante che ne deriva è stata l’analisi delle cause e la conseguente individuazione di attività di miglioramento dedicate alla riduzione dei mancanti. Nel caso specifico, in breve tempo, sono stati avviati alcuni progetti e implementati strumenti operativi per:
- la gestione ed il tempestivo ripristino del materiale scartato per problemi di qualità, gestendo le urgenze avendo come riferimento il piano di assemblaggio;
- il miglioramento della procedura di gestione della spedizione dei ricambi in modo da evitare la “cannibalizzazione” dei componenti destinati all’assemblaggio;
- l’impostazione di un piano di consegna per i verniciatori esterni sincronizzato con il piano di assemblaggio.
È sicuramente importante sottolineare che, condizione necessaria per il successo di questo tipo di attività, è la collaborazione delle diverse funzioni aziendali coinvolte (vendite, produzione, approvvigionamenti, qualità per la gestione degli scarti/ripristini e azioni correttive nei confronti del fornitore).
Si può concludere osservando che, dopo alcuni mesi di applicazione di questa procedura, un tale approccio ai mancanti permette di focalizzarsi sulle reali urgenze dell’azienda garantendo minori disservizi alla produzione e intercettando con anticipo i problemi.
In caso di ritardi nella consegna Italcab è ora in grado di informare per tempo i clienti che stanno apprezzando le informazioni, anche se negative. Allo stesso tempo i clienti hanno percepito un beneficio in termini di servizio (puntualità di consegna) migliorato sia grazie al processo appena descritto sia grazie a tutta un'altra serie di azioni di miglioramento del sistema di pianificazione di cui parleremo nei prossimi articoli.
Riproduzione riservata©