La funzione del Planning ricopre un ruolo strategico all’interno di ogni azienda perché governa il flusso informativo sia all’interno che verso l’esterno dell’organizzazione. Si interfaccia, inoltre, con tutti gli attori lungo la Supply Chain: dai fornitori ai clienti, passando attraverso i reparti produttivi, il magazzino e fino alle spedizioni.
Lo scopo ultimo di chi si occupa di pianificazione è garantire il massimo livello di servizio al cliente, mantenendo al tempo stesso un corretto e adeguato valore di stock e un buon livello di efficienza, sia in fabbrica che negli uffici. Il bilanciamento tra le maggiori voci di costo e il livello di servizio concordato rappresenta per l’azienda un obiettivo sfidante e complesso ed è per questo motivo che necessita di processi idonei e strutturati. Occorre agire a due livelli:
- Strategico, per strutturare al meglio il processo di pianificazione aggregata che unisce le informazioni provenienti dal mercato con i vincoli propri delle Operations (su tutti, la capacità produttiva e il reperimento dei materiali)
- Operativo, per riallineare la Supply Chain alla domanda attraverso l’introduzione di strumenti specifici, come lo Stock Profiling.
Il modello di gestione delle scorte (Stock Profiling)è uno strumento utile per dimensionare e aggiornare frequentemente e in maniera massiva i parametri di pianificazione, quali scorte di sicurezza, lotti minimi e multipli, previsioni di consumo ecc.
Sappiamo quanto negli ultimi anni sia cambiato il mercato; per questo motivo il pianificatore deve necessariamente aumentare la frequenza di aggiornamento dei parametri non solo per garantire un adeguato allineamento alle esigenze che possono cambiare molto rapidamente, ma anche per intercettare variazioni della domanda e agire di conseguenza su una corretta parametrizzazione.
Gestione delle scorte: come funziona?
Vediamolo insieme seguendo il flusso dello schema rappresentato di seguito:
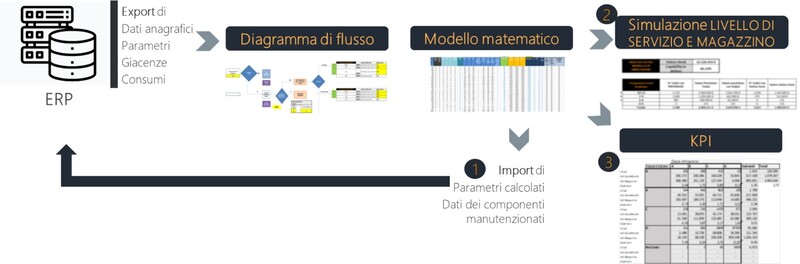
- Da ERP, si esportano gli attuali dati di pianificazione relativi ai componenti sui quali definire i nuovi parametri.
- Si costruisce un diagramma di flusso che tenga conto di tutte le variabili e delle relazioni che vogliamo considerare in fase di dimensionamento dei parametri: ad esempio, la classe ABC di valore/frequenza di appartenenza, se è un ricambio oppure no, se è specifico di un cliente, se sono presenti programmi per i mesi futuri, se è già prevista una scorta di sicurezza su articolo padre, ecc. Il diagramma rappresenta uno schema logico con un duplice scopo:
- mettere in fila tutti questi elementi e definire le logiche di dimensionamento;
- esplicitare chiaramente le regole di pianificazione (a volte complesse e intricate) per condividerle anche al di fuori della funzione planning.
- Si “traduce” il diagramma di flusso con tutte le logiche in un modello matematico che permetta di calcolare in modo massivo i parametri per ogni codice.
- Le simulazioni e i KPI permettono di analizzare le scelte fatte sul diagramma di flusso e di valutarne gli impatti. Una volta validata l’opzione preferita si può procedere con l’import su ERP dei parametri dimensionati (che dovranno essere manutenuti regolarmente).
A seconda delle esigenze e della complessità si procede su diversi perimetri ben identificati, evitando un eccessivo immobilizzo causato dall’eventuale duplicazione delle scorte e massimizzando il livello di servizio. Lo strumento può essere infatti replicato e adattato in base alle necessità e i perimetri d’azione. Ad esempio:
- diversi livelli di Distinta Base: materie prime, semilavorati, prodotti finiti
- specifici range di clienti: direzionali, strategici ecc.
- magazzini centrali e distributivi
- business caratteristici, come ad esempio i ricambi.
Gestione delle scorte: un caso di applicazione aziendale
Vediamo ora, in sintesi, un’applicazione reale e i risultati raggiunti. Ci troviamo nella sede di distribuzione italiana di un’azienda tedesca, leader mondiale nella produzione di accessori per mobili.
L’esigenza dell’azienda è quella di definire i corretti livelli di stock per uno specifico perimetro di clienti servito interamente dall’Italia con il duplice obiettivo di migliorare il servizio e di ridurre i costi logistici e di movimentazione dal magazzino centrale in Germania.
Partendo da questa finalità abbiamo sviluppato lo Stock Profiling perimetrato sui clienti individuati, andando ad analizzare nel dettaglio i loro consumi ed eventuali picchi stagionali e dimensionando di conseguenza i parametri di pianificazione. Questo ha garantito scorte di sicurezza dedicate e lotti minimi di approvvigionamenti con minori costi logistici e con un incremento del livello di servizio.
Al fine di validare gli output proposti dal modello matematico, abbiamo individuato due indicatori di simulazione dei risultati attesi: il valore dello stock futuro e l’ingombro fisico di magazzino.
Le simulazioni hanno consentito di definire, da un lato, un target accettabile di incremento del valore d’immobilizzo; dall’altro, di rivedere alcune specifiche di stoccaggio e di individuare materiale obsoleto da smaltire per far spazio alle nuove necessità.
Una volta importati massivamente su ERP i nuovi parametri, abbiamo messo sotto controllo i risultati attraverso una serie di indicatori specifici:
- valore dello stock (confrontato con il target simulato nello Stock Profiling)
- indice di saturazione di magazzino
- costi logistici complessivi: pick-pack-ship dalla Germania e costi di spedizione dall’Italia
- livello di servizio in termini di puntualità rispetto alla data confermata tramite l’On Time Delivery (OTD).
Visti i buoni risultati raggiunti sui primi clienti (+10% OTD, -1,5% costi logistici) abbiamo allargato il perimetro portandolo dapprima a 30 nell’arco dei successivi dodici mesi, fino agli attuali 60.
I vantaggi della gestione delle scorte
Possiamo di seguito sintetizzare i principali vantaggi dello Stock Profiling:
- velocità e affidabilità: lo Stock Profiling permette di non perdersi nella complessità di questa attività che, se fatta in modo destrutturato, richiederebbe molto tempo
- visione d’insieme tramite l’aggiornamento massivo: l’obiettivo è infatti di coprire almeno l’85-90% dei codici, focalizzando l’attenzione sui restanti, gestiti tramite eccezioni perché altamente critici
- simulare i risultati attesi sia in termini di stock (valore economico e ingombri) che di livello di servizio
- esplicitare e condividere le basi della pianificazione che, diversamente, rimarrebbero solo nella testa di chi si occupa di pianificazione.
In conclusione, attraverso la configurazione corretta del modello di gestione delle scorte è possibile dimensionare correttamente i parametri di pianificazione, garantire il giusto livello delle scorte di magazzino, ridurre al minimo i lotti di approvvigionamento, il tutto finalizzato al miglioramento del livello di servizio al cliente e all’ottimizzazione dell’efficienza operativa.
Riproduzione riservata©