Qual è il grado di efficienza con cui sto producendo?
Sto sfruttando nel modo giusto il mio reparto produttivo?
Ho capacità produttiva disponibile per portare a casa nuovi prodotti?
Non di rado, nei progetti di miglioramento della produzione ci vengono poste queste domande. La risposta può che essere unica per tutte: implementiamo il metodo OEE e vediamo su cosa agire; ovvero, prima misuriamo e poi capiamo dove e quanto migliorare.
Cosa è l’OEE?
Dal punto di vista accademico, OEE significa “Overall Equipment Effectiveness”, ovvero Efficienza Globale dell’intero Impianto. È un indicatore percentuale che rappresenta il rendimento di una risorsa o di un reparto produttivo composto da più risorse (siano esse macchinari o risorse umane) in un determinato periodo di tempo.
Facciamo un esempio: il macchinario X lavora per una settimana su un unico turno di 8 ore. Il macchinario X quindi è a disposizione del reparto produttivo per 40 ore (calcolato come: 5 giorni per 8 ore/giorno = 40 ore). Se l’OEE iniziale dovesse risultare pari al 50% significa che il macchinario ha lavorato per la metà del tempo disponibile; ovvero, tradotto in termini pratici, il numero dei pezzi buoni prodotti sono stati la metà rispetto alla sua capacità massima teorica.
Per come viene calcolato, l’OEE fa emergere inevitabilmente tutte le inefficienze che possono caratterizzare un sistema produttivo e che spesso si tende a non vedere, per diverse ragioni.
Queste inefficienze possono portare a una riduzione importante del rendimento produttivo come ad esempio troppi attrezzaggi/setup, fermi macchina (ad esempio mancanza dell’operatore, micro-fermate o guasti), pianificazione della produzione mancante o non tempestivamente condivisa/rilasciata, prodotti non conformi, e così via.
In questo articolo vedremo cosa significa inserire l’OEE favorendo il processo decisionale in modo mirato e ponderato, oltre a controllarne gli effetti nel tempo sulla produzione.
Per come calcolare l'OEE esistono molteplici formule e il modello “classico” si può adattare sicuramente bene in contesti dove si hanno linee produttive automatizzate o assemblaggi manuali e la presenza di tutti i dati necessari al calcolo (come per esempio tempi di produzione, tempi di setup e così via).
Per cui la formula dell’OEE sarà: OEE = Disponibilità x Prestazione x Qualità
L’OEE è dunque il prodotto di tre indicatori percentuali che impattano sulla performance del reparto produttivo:
- Disponibilità: percentuale relativa all’effettivo tempo di lavoro sul totale del tempo disponibile (le 40 ore dell’esempio iniziale)
- Prestazione (o rendimento): percentuale di pezzi prodotti rispetto alla potenzialità teorica dell’impianto (velocità nominale rispetto l’effettiva)
- Qualità: percentuale di pezzi buoni sul totale dei pezzi prodotti.
Teoricamente e in una situazione ideale, per avere un OEE pari al 100% l'impianto dovrebbe lavorare tutto il tempo e alla velocità massima, produrre pezzi perfetti senza creare mai scarti. Ma come ben sappiamo, tutto questo è praticamente impossibile perché i macchinari, seppur nuovi o in ottimo stato, possono subire degli arresti (per micro-fermate o guasti) e generare prodotti difettosi.
Le variabili che causano questi problemi vengono classificate come “perdite produttive” e possono essere identificate in modo macro secondo questo schema:

Per rendere ancora più efficace il metodo è necessaria una rilevazione puntuale delle informazioni: non solo quelle delle produzioni effettive ma, soprattutto, quelle relative alle perdite di efficienza in modo da:
- individuare qual è la variabile che influenza di più il nostro indicatore
- attuare delle azioni correttive mirate
- controllare che quanto stabilito porti realmente a un miglioramento del rendimento produttivo.
Non sempre però il tempo a nostra disposizione ci consente di applicare il metodo: l’esigenza dell’azienda è spesso quella di ottenere risultati rapidi garantendo il controllo sulla produzione nel tempo. In casi come questi viene solitamente applicato un secondo metodo di calcolo OEE.
OEE= Tempo redditizio / Tempo disponibile
dove:
- Tempo redditizio rappresenta il tempo al quale il cliente/mercato riconosce un valore.
- Tempo disponibile è la disponibilità oraria di presenza in azienda delle risorse (in caso di operatori) o di apertura impianto (in caso di macchinari, ovvero il tempo in cui la macchina è “disponibile” a lavorare). A questa categoria è decisamente più semplice e immediato associare un costo.
Si può, quindi, introdurre il concetto di Tempo Standard o Tempo di Riferimento che rappresenta il tempo necessario a svolgere una determinata attività al netto di eventuali perdite di efficienza e dopo aver individuato un metodo di lavoro condiviso e comune.
Il Tempo Standard è definito dall’azienda per lo specifico ciclo di lavoro (sia esso prevalentemente manuale o automatico o un insieme dei due) ed è solitamente ritenuto come “giusto” per svolgere una determinata attività.
Nel caso di produzioni prevalentemente automatiche, il Tempo Standard è coincidente con il Tempo Ciclo del macchinario mentre, nel caso di attività manuali come ad esempio l'assemblaggio, è più complesso definirlo in quanto è necessario applicare le tecniche dei Tempi e Metodi.
La registrazione delle attività di produzione e delle eventuali “perdite di efficienza” avviene inizialmente in formato cartaceo. Questo, nel breve tempo, può aumentare il tempo perso per registrare tutti i dati raccolti ma, in realtà, è funzionale all’individuazione ed ottimizzazione di un format che potrà essere preso in carico dai diversi sistemi informatici nati per supportare queste attività, come ad esempio il MES (Manufacturing Execution Systems).
Il MES è un sistema che permette di gestire e controllare la produzione di un’azienda: dalla gestione degli ordini di produzione relativamente ai relativi avanzamenti (in termini di tempo e quantità), al versamento in giacenza nonché al collegamento diretto ai macchinari per il controllo della produzione stessa.
Grazie ai MES, la tempestività con cui i dati si rendono disponibili e la relativa robustezza/attendibilità delle informazioni permette ai responsabili di produzione di accorgersi di eventuali problemi in fase di registrazione o di perdite di efficienza importanti durante il flusso produttivo in modo da intervenire tempestivamente.
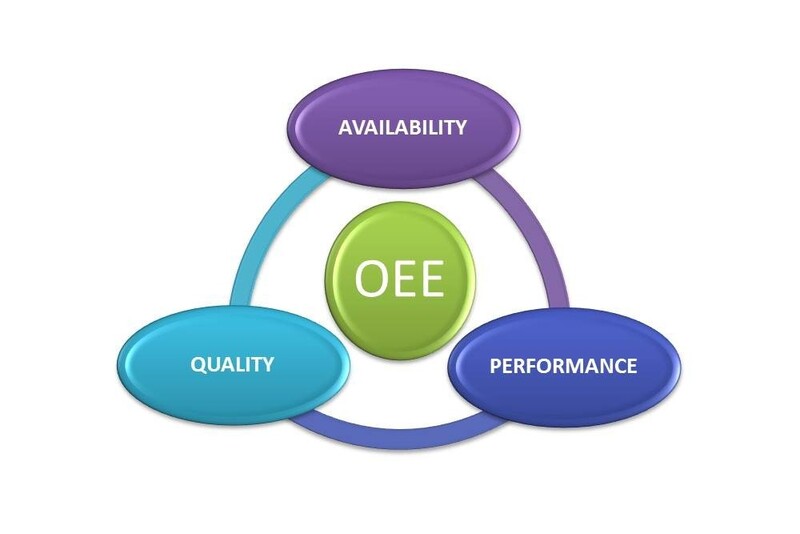
Considerazioni finali
Solitamente aziende che non hanno mai affrontato progetti di miglioramento guidati dai metodi appena descritti hanno un OEE iniziale attorno al 50-60%; basti pensare che i migliori produttori (tra cui anche Toyota) si attestano con un OEE intorno all’85-90% (obiettivo ritenuto “World Class”).
Raggiungere il 100% è impossibile perché ogni macchinario necessita di attrezzaggi/setup o può subire dei guasti, mentre gli operatori sono soggetti a perdita fisiologica durante il giorno di lavoro.
Nel caso in cui l’OEE dovesse risultare maggiore del 100% significa che i Tempi Standard sono stati sovrastimati e quindi necessiterebbero di una revisione.
Il calcolo del solo OEE non implica necessariamente un miglioramento della produttività. Occorre, infatti, abbinare un percorso strutturato di miglioramento che utilizzerà questo indicatore per monitorare gli sviluppi “KPI-OEE percorso".
Raggiungere in poco tempo e con investimenti ridotti un OEE dell’85% partendo dal 60% significa aumentare la propria efficienza produttiva di 42 punti percentuali, ovvero, in altre parole, significa essere in grado di produrre di più a parità di risorse.
Per concludere, due sono le macro-leve su cui spingere maggiormente per aumentare l’OEE:
- gestione tecnica delle risorse, ovvero introdurre una pianificazione più strutturata
- gestione organizzativa del reparto produttivo, ovvero maggiore sensibilizzazione al controllo e ai risultati raggiunti: aspetti che, di solito, vengono dati per scontati, ma che sono alquanto rilevanti per far sì che il modello dell’OEE diventi la base di un nuovo modo di lavorare
Infine, ritengo fondamentale che il risultato venga condiviso non solo con il responsabile di reparto, ma anche con tutti gli operatori. Comprendere il senso delle cose e, nello specifico, degli indicatori permette di capire l'importanza di raccogliere in modo puntuale dati corretti affinché il risultato sia significativo e realistico. L’affidabilità dei dati agevola, di conseguenza, una maggiore velocità di implementazione del processo di miglioramento in fabbrica.