Siamo sicuri che la misurazione delle performance aziendali abbia sempre, come diretta conseguenza, un miglioramento delle prestazioni o dei processi?
Tempo fa, nel corso di una riunione avanzamento progetto, un manager affermò con grande convinzione quanto segue: “La prossima volta, prima di introdurre degli indicatori di efficienza in fabbrica, ci penserò due volte. Mi sembra che possano essere controproducenti”.
Tale frase mi spiazzò decisamente in quanto in apparente contraddizione con tutto quello che l’esperienza di vent’anni di lavoro mi ha portato a credere.
“Perché?” chiesi, curioso di capire le sue motivazioni.
Risposta: “Perché quando gli indicatori non vanno bene, nessuno fa nulla, né dice nulla, né sembra preoccupato. Alla fine, rischia anche di passare il messaggio … che anche se l’efficienza è KO, alla fine va bene comunque. Almeno prima, non conoscevamo la nostra situazione. Meglio prima migliorare, poi iniziare a misurare”.
È questo un classico esempio in cui, probabilmente, il percorso di introduzione del OEE utilizzato non è stato del tutto corretto e che mi ha dato lo spunto per raccontare quali siano i passi necessari per inserire in modo efficiente una metrica importante (o meglio, indispensabile) come l’OEE; passi che, ritengo, siano validi per tutti i KPI, se vogliamo che siano realmente utili.
Focalizziamoci ora su un ambito specifico, un reparto di lavorazione.
I prerequisiti, in questo caso, sono davvero minimi. Tecnicamente occorre avere a disposizione il database dei tempi standard di lavoro ed un sistema informatico di raccolta dati in fabbrica. Errato pretendere a priori un alto livello di qualità del dato: sarà l’introduzione della metrica che faciliterà, come conseguenza, il miglioramento dei dati e delle informazioni necessarie e non il contrario. Nell’articolo “Come mettere sotto controllo l’efficienza della fabbrica in soli due mesi” potrete avere una idea più precisa al riguardo.
Rispetto alle persone, unico prerequisito è, come sempre, spiegare a cosa serve un KPI e come si utilizza. Anche qui, nulla di nuovo a patto che si facciano alcuni precisi passi su organizzazione, persone e strumenti.
Vediamo quali.
- Automazione della raccolta dati – Ore lavorate, quantità prodotte, scarti
Quantità prodotte (pezzi buoni e scarti) e relative tempistiche. La tecnologia a disposizione, attraverso sistemi MES sempre più accessibili e performanti, certamente è di grande aiuto. In ogni caso è richiesto un lavoro per rendere affidabile la raccolta dati, sia per le ore che per le quantità prodotte. Rimane ancora un tema di elevati costi per collegare il sistema di raccolta dati alle macchine, ma su questo osservo una evoluzione rapida in questi ultimi anni.

- Procedura per la manutenzione dei tempi standard – Responsabilizzazione del caporeparto
Nel corso del tempo i tempi standard tendono a disallinearsi rispetto alla realtà (in meglio se si lavora per migliorare, in peggio negli altri casi) e occorre quindi dotarsi di procedure snelle per assicurarne la corretta manutenzione. Si tratta di una formidabile arma di responsabilizzazione dei capireparto e, dove presente, della funzione Tempi e Metodi.
Importante al riguardo è definire il rapporto uomo/macchina. Ricordate che OEE manodopera può essere in alcuni casi più importante del OEE macchina (ad esempio quando il mercato è in flessione).
- Monitoraggio ore di presenza della manodopera
Il responsabile di reparto deve avere a disposizione tutti i giorni il consuntivo delle ore di presenza della manodopera, suddivise tra unità dirette ed indirette, e per funzione di supporto (attrezzisti, addetti alla movimentazione, manutentori). Ricordate che il denominatore dell’OEE Manodopera è dato dalle ore di presenza.
- Controllo della sovrapproduzione
Problema: una volta introdotta la metrica dell’OEE, presto il responsabile di reparto scoprirà che un’arma a sua disposizione per migliorarlo sarà la sovrapproduzione (“produco più del richiesto, alla peggio userò più avanti i pezzi, intanto ottimizzo”). Ogni scusa sarà buona per questo scopo. Niente di peggio se volete innescare il miglioramento. Quindi occorre introdurre il report che verifica il rispetto delle quantità previste, evidenziando in modo diretto le quantità prodotte in eccesso per massimizzare OEE ma non richieste dalla programmazione.
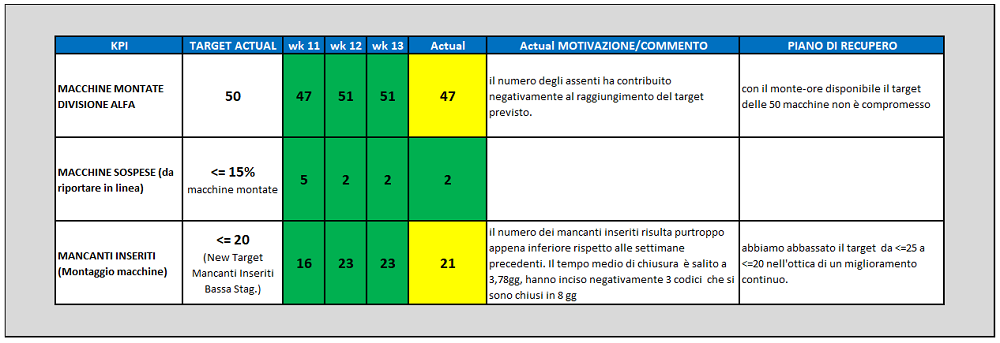
- Pianificazione del carico di lavoro macchine e persone
La mole di informazioni a disposizione dell’azienda non sempre è garanzia di un buon uso delle stesse. In alcuni casi si riescono anche a fare delle analisi, ma spesso il tool utilizzato (anche un semplice file excel) non risulta ottimizzato. È importante avere un sistema che evidenzia il carico di lavoro per le macchine e per le persone. Anche questo aspetto è necessario per consentire la taratura sistematica delle ore di presenza della manodopera (diretta ed indiretta) in base al carico di lavoro. Un sistema OEE senza lo strumento per la valutazione dei carichi risulta incompleto rispetto ad uno degli scopi principali: mantenere efficienza anche in caso di variazione sui volumi prodotti. Strumenti semplici ed indicativi nel tempo convergeranno.
- Pubblicazione degli indicatori e quick meeting di reparto – Visual Management
Senza la pubblicazione sistematica gli indicatori perdono di significato. Ma qual è una frequenza corretta per la pubblicazione e quali le modalità più efficaci? Per quanto riguarda il primo punto il minimo è la settimana anche se siamo tutti consapevoli che in un reparto il giorno o addirittura il turno è l’orizzonte corretto per analizzare l’efficienza e fare le opportune considerazioni. Per quanto invece riguarda le modalità di pubblicazione, la bacheca, o meglio il Monitor TV o, per chi ha spazio, una “war room” attrezzata e dedicata, sono gli strumenti attraverso i quali gli operatori guardano i dati e definiscono con il capoturno/caporeparto le azioni.
È importante definire uno standard delle metriche chiaro ed immediato anche se, per gli addetti ai lavori, potrete permettervi una versione più articolata. Molta attenzione occorre prestare alla definizione dei target (possiamo usare dei benchmark o lo storico) e alla definizione del report, che deve essere compilato in base al dato settimanale: in quali casi la fabbrica è “obbligata” ad attuare un’azione di miglioramento? Ricordate l’osservazione del manager ad inizio di questo articolo.
Avvio azioni di miglioramento
È il risultato finale del percorso, ve lo sarete meritato e non tarderà ad arrivare se avrete seguito e messo in pratica correttamente i 6 passi. Come detto, la definizione di un target per il miglioramento è la condizione minima per innescare il processo. Non è difficile avendo a disposizione l’OEE. Suggeriamo, a livello di reparto, di definire dei “Target Step” incrementali tra il 5% ed il 10% ogni sei mesi, per i primi 3-4 semestri, a seconda del punto di partenza; poi il miglioramento diventa decisamente più graduale e meno gravoso
Una considerazione finale (politicamente scorretta)
Si può migliorare una fabbrica anche senza misurare l’OEE? Certo, ma l’esperienza mi dice che rendere oggettivo il miglioramento attraverso una metrica seria e severa come l’OEE rende più concreto il compito di chi deve ottenere risultati.
Mi è capitato di vedere attuate azioni percepite dalle persone come “miglioramento” che non hanno però avuto un impatto positivo sull’indicatore oppure lo stesso è stato trascurabile. Questo a volte complica anche il lavoro dei consulenti, ma lo rende sicuramente più interessante. La sfida dell’efficienza è lanciata. Potremmo dire provocatoriamente: no OEE, no miglioramento.