Nell'era della trasformazione digitale e di Industria 4.0 ha ancora senso parlare di Lean Production?
Crediamo che la risposta sia affermativa anche perché la trasformazione digitale non si realizza solo attraverso l'introduzione di tecnologia. Anzi, limitarsi unicamente a questo aspetto rischia di compromettere in maniera determinante la competitività aziendale. Il tema della trasformazione digitale (che nel settore manifatturiero ha preso il nome di Industria 4.0) ha avuto il merito di riaccendere i riflettori sul settore industriale. D'altra parte, questa ondata di novità tecnologiche ha da subito messo in evidenza una criticità: in assenza di una idea molto precisa di come la tecnologia possa essere funzionale a raggiungere gli obiettivi aziendali, la possibilità di fare danni è molto elevata (con spreco di tempo e denaro).
A questo punto è lecito chiedersi se la Lean Production, ovvero quell’approccio culturale e metodologico volto a favorire il raggiungimento dell’eccellenza nei processi operativi, possa anche consentire all’azienda di cogliere i vantaggi della digitalizzazione, anche alla luce di una storica diffidenza dell’approccio Lean verso la tecnologia e l’automazione.
Lean Production e Industria 4.0 mostrano diversi punti di contatto: l'orientamento ai processi, l'attenzione ai dati come base per il miglioramento, la centralità delle persone e la conoscenza diffusa.
L'introduzione di tecnologie deve perciò favorire gli stessi identici obiettivi e questo può accadere solo se perfettamente integrata con le persone e i processi aziendali.
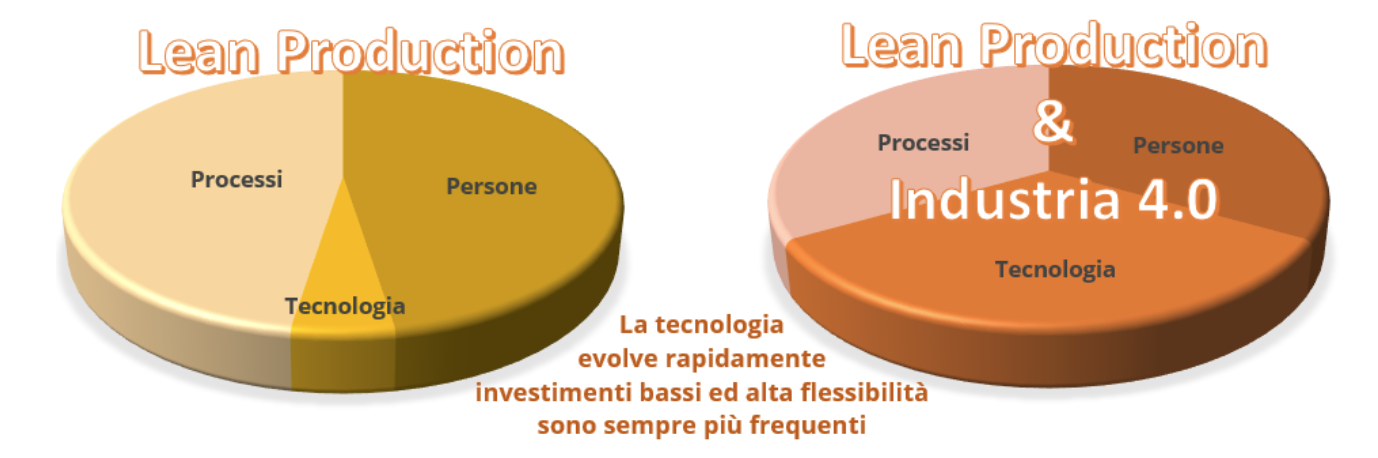
La Lean Production (più propriamente Lean Manufacturing) rappresenta ancora oggi il sistema più efficace per la gestione di aziende non solo in ambito manifatturiero.
La “Produzione Snella” nasce negli anni '50 in Toyota quando Taiichi Ohno, padre fondatore di questo sistema di produzione, comprende la necessità di utilizzare al meglio le poche risorse disponibili a causa della guerra appena terminata. L’obiettivo di incrementare l’efficienza della fabbrica diventava condizione necessaria per garantire la competitiva dell’azienda. Da qui il famoso detto a lui riconducibile: "fare di più con meno".
Nei primi anni ’90 gli studiosi J.P. Womack e D.T. Jones studiarono e compresero le potenzialità di questa filosofia tanto da codificarla e generalizzarla ai fini della divulgazione nel mondo occidentale. È da qui che nasce il termine “Lean Production” o “Produzione Snella” con il quale si fa riferimento ad un approccio aziendale che punta al miglioramento continuo e costante dei processi operativi. La finalità è quella di servire al meglio il cliente attraverso l'individuazione e l’eliminazione degli sprechi che si nascondono nei processi operativi. La parola chiave è “flusso”: flusso delle informazioni e flusso dei materiali.
I benefici attesi:
- diminuzione dei tempi di consegna (livello di servizio al cliente)
- riduzione dei costi di produzione ed aumento dell'efficienza delle risorse
- riduzione dei tempi di attraversamento
- miglioramento della qualità di prodotti, dei servizi e dei processi
- riduzione delle scorte intermedie e finali
- aumento della flessibilità (intesa come capacità di risposta) in presenza di variazioni del mix della domanda
A differenza di quanto si pensi, il sistema TPS (Toyota Production System) nasce in un contesto di ampia varietà di gamma e bassi volumi; situazione questa che rispecchia molto l'attuale contesto economico dove il cliente chiede sempre più prodotti su misura anche ad aziende che facevano della standardizzazione il loro punto di forza. Da qui la storica diffidenza verso le automazioni e la tecnologia, spesso causa di rigidità in produzione, in contraddizione con la flessibilità e agilità richiesta in presenza dei cambiamenti micro e macro del mix della domanda. L’evoluzione della tecnologia sta radicalmente trasformando tale criticità: si pensi, ad esempio, alle automazioni (sia industriali che informative) sempre meno costose e più facilmente implementabili.
I cinque principi base a fondamento della Lean Production sono apparentemente molto semplici. Tuttavia, se correttamente interpretati, guidano attraverso un percorso metodologico molto chiaro e ben definito.
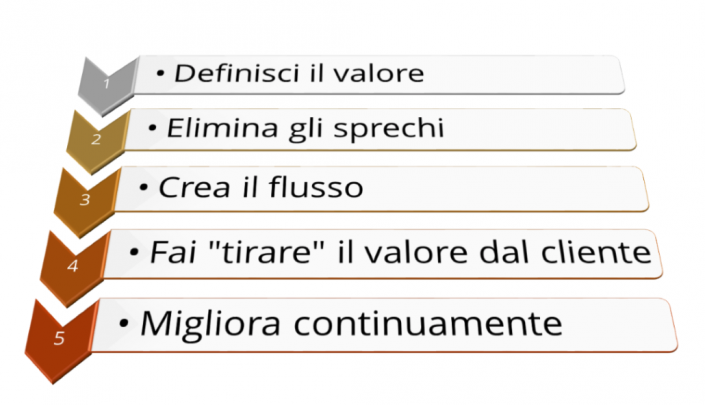
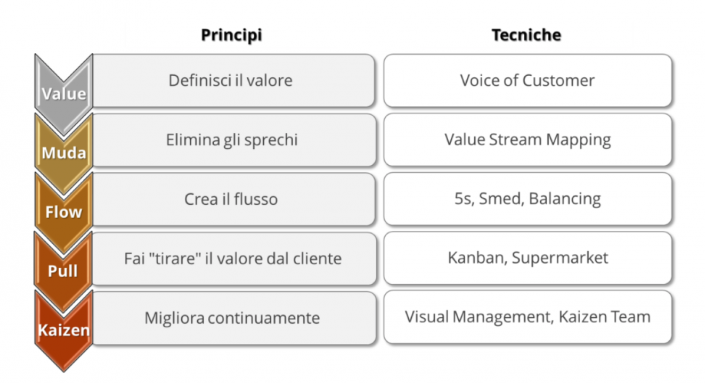
Tali principi non sono esclusivi solo della fabbrica, ma trovano altrettanta ed efficace applicazione anche nel mondo della gestione delle informazioni ovvero dei processi gestiti tipicamente dagli uffici, anche di aziende manifatturiere e, in generale, delle aziende che offrono servizi al mercato (in questo caso si parla di Lean Office o meglio di Lean Service).
Anche se i principi e le tecniche Lean sono applicate ormai da tempo, il sistema tradizionale di produzione (denominato “per lotti e code”) continua a resistere in molte aziende del nostro Paese, nonostante il contesto competitivo nazionale e internazionale sia decisamente cambiato. Riduzione generalizzata dei volumi e dei tempi di consegna, ampliamento della gamma spingono le aziende sempre più a lavorare con una logica a “flusso”. Ma senza un metodo preciso di intervento la trasformazione Lean rischia di fallire.
Riproduzione riservata©