Nel corso dei sopralluoghi che solitamente effettuiamo all’interno dei reparti produttivi, riscontriamo spesso situazioni poco chiare, se non addirittura critiche, relativamente al materiale che deve alimentare le linee o le aree di operative (Material Handling): non di rado constatiamo la sua mancanza al momento richiesto; in altri casi il materiale, pur presente presso la postazione di lavoro, vi staziona in modo disordinato oppure non reca la corretta indicazione della sua destinazione.
Nei casi come quelli citati le aziende curano poco o non curano affatto il Material Handling ovvero quella disciplina che studia lo stoccaggio e la movimentazione dei materiali e che, attraverso l'impiego di opportuni metodi e strumenti, consente di avere la giusta quantità del giusto materiale nel posto giusto rispettando tempi, sequenze, condizioni richieste e minimizzando i costi.
Una errata o poco accurata movimentazione dei materiali infatti, impatta sull’efficienza della manodopera diretta costretta ad andare alla ricerca del materiale e portarlo in prossimità del centro di lavoro. Nel tempo, le aziende hanno preferito orientarsi verso la ricerca di soluzioni tecniche al problema, cercando di recuperare efficienza attraverso una riduzione dei tempi ciclo. Tuttavia, non quantificando e non monitorando la componente di movimentazione si generano costi indiretti e costi fissi (ad esempio l’impiego di ulteriori risorse e mezzi di movimentazione).
Per esperienza, questa situazione crea spesso tensioni interaziendali: tipicamente l’area produttiva attribuisce agli operatori della logistica interna la responsabilità di tali mancanze. A nostro avviso la verità è una sola: in queste aziende mancano le regole oltre che un ben definito flusso informativo che guidi gli operatori indiretti nella movimentazione di materiale. Manca cioè una corretta applicazione del Material Handling.
Presentiamo quindi il caso della Italcab Spa dove è stato possibile ridurre le perdite legate alla movimentazione dei materiali introducendo un flusso informativo di supporto agli operatori nel reparto di carpenteria.
Italcab Spa è azienda leader nella progettazione e produzione di macchine movimento terra e industriali, in particolare cabine operatrici ad alto livello di comfort e funzionalità. Ha sede a Monastier di Treviso.
Come mostrato nell’immagine sottostante, il reparto di carpenteria è suddiviso in tre macro-lavorazioni principali (taglio laser, separazione lamiere, piegatura) a cui si aggiungono altre lavorazioni secondarie. È importante sottolineare che, data la natura della lavorazione, non tutti i pezzi che vengono separati devono essere piegati: ma alcuni di questi rimangono “dritti” per essere portati in area di imballo e successivamente alla saldatura.
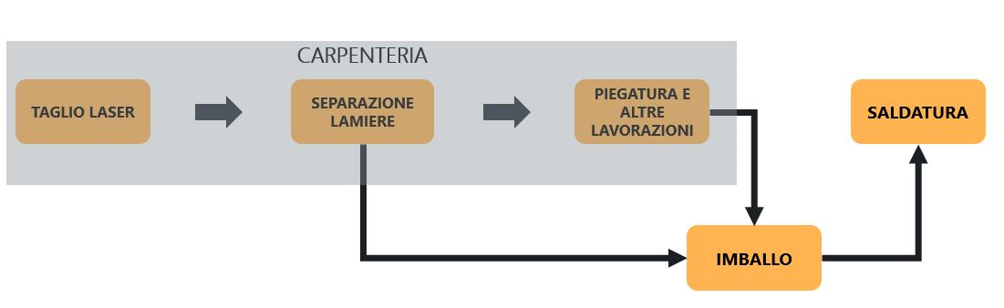
In fase di separazione delle lamiere la mancanza di un’istruzione guidata riguardo alla prima destinazione dei componenti faceva sì che gli operatori creassero dei bancali che contenevano pezzi con destinazione diversa. Ad esempio, sullo stesso bancale erano presenti pezzi che dovevano rimanere dritti e altri che dovevano essere piegati; questo generava inefficienze legate alla movimentazione del componente verso la sua corretta destinazione o errori di lavorazione (per esempio prodotti che dovevano rimanere dritti venivano portati in area di piegatura).
L’obiettivo che ci siamo posti è stato quello di facilitare la movimentazione del materiale all’interno del reparto di carpenteria attraverso la condivisione di uno standard univoco di separazione dei materiali. In altri termini, in accordo con il team di cui facevano parte i vari responsabili aziendali, partendo dalla fase di separazione lamiere, abbiamo introdotto un metodo che agevolasse gli operatori nella creazione di bancali con componenti aventi la stessa destinazione.
Come riflessione personale, tengo a sottolineare che tutte le aziende con un reparto di carpenteria possono orientarsi verso questa soluzione, ma la tipologia di lavorazione per commessa di Italcab ha spinto il team di progetto ad andare un po’ oltre. Infatti, essendo i programmi di taglio sempre gli stessi, è stato possibile capire per ogni lamiera quali fossero i pezzi da separare, quali le loro dimensioni, il peso e la destinazione finale. Di conseguenza, per ogni programma di taglio era già evidente, a monte:
- la tipologia del bancale e la sua quantità;
- la tipologia e la quantità dei contenitori da utilizzare per stoccare i pezzi separati;
- la destinazione dei pezzi.
Per ogni programma di taglio, era già chiaro quali fossero i pezzi da collocare sui bancali e quale fosse la loro destinazione, tenendo conto dei vincoli di peso dei contenitori da movimentare.
Ma come scaricare in reparto queste informazioni e passarle in modo semplice agli operatori?
Osservando le attività svolte quotidianamente dagli operatori, ci siamo posti alcune semplici domande:
- Quanti bancali, quanti contenitori e di quale tipo?
Per ogni programma di taglio viene generata un’istruzione di setup della postazione (Bolla Nesting) che, oltre ad associare i codici ai pezzi presenti sulla lamiera da separare, comunica all’operatore la quantità e il tipo di bancali e di contenitori da portare in postazione.
- Quali codici vanno sul bancale e come identifico il bancale e la sua destinazione?
La Bolla Bancale è un’istruzione che comunica all’operatore quali siano i contenitori e i pezzi che vanno depositati sul bancale appena portato in postazione. Lo stesso documento identifica il bancale con un codice e la sua destinazione (in questo caso univoca).
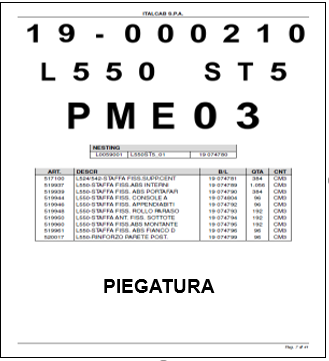
3. Come identifico i prodotti smistati?
Attraverso la Bolla Semilavorato si ha la possibilità di identificare il prodotto separato attraverso il disegno tecnico, associarlo al codice identificativo e posizionare il pezzo all’interno del contenitore sul bancale di riferimento.
L’introduzione e l’applicazione di queste semplici istruzioni hanno portato ordine tra la fase di separazione lamiere e quella di piegatura/altre lavorazioni. Il principale risultato ottenuto è stato quello di ridurre del 40-50% il Material Handling in carico al caporeparto e agli operatori indiretti.
Per quanto visto, trascurare il Material Handling può generare grosse inefficienze che, d’altro canto, possono essere recuperate con semplici interventi organizzativi ed informativi.
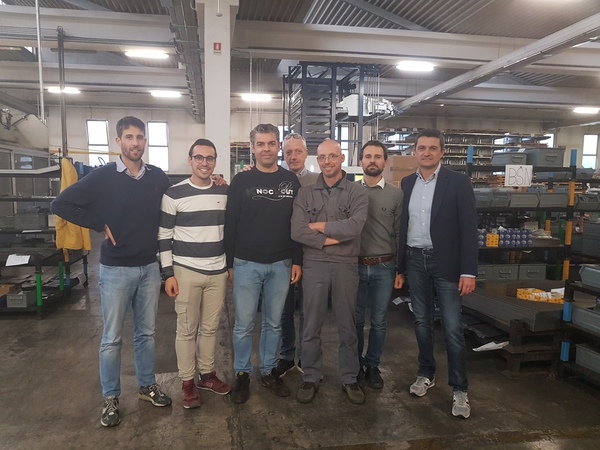
Riproduzione riservata©