L’attuale contesto economico e commerciale richiede sistemi logistici sempre più performanti in termini di livello di servizio fornito e di efficienza. La gestione corretta delle risorse a disposizione in magazzino è tra i fattori chiave per il raggiungimento di questi obiettivi.
Per gestione “corretta” si intende l’allocazione e il dimensionamento dinamico delle risorse nelle diverse aree di magazzino in base al carico di lavoro del momento e alle priorità date.Se si genera una coda di lavoro in area accettazione per un picco negli ingressi, devo intervenire per spostare risorse da altre aree verso questa per evitare accumuli che potrebbero impattare sulla disponibilità del materiale per le fasi operative successive. Se “diminuisce” il carico di lavoro in fase di prelievo, posso allocare ad altre mansioni i pickeristi evitando che si inneschino dei tempi morti di attesa.
Se viene comunicata una priorità di preparazione per alcuni ordini cliente, posso “rafforzare” l’area con risorse allocate in processi al momento non critici o a bassa priorità.
La nostra esperienza ci insegna che, in molte realtà, le risorse sono spesso gestite in maniera statica, mantenendo un costante numero di operatori nelle diverse aree indipendentemente dai loro carichi di lavoro, con conseguente generazione di colli di bottiglia che sono fonte:
- di ritardi e/o di mancato rispetto delle priorità date
- di inefficienze, errori o degrado della qualità legate al tentativo di ridurre la coda di lavoro
L’allocazione dinamica delle risorse in maniera continuativa in base ai carichi di lavoro effettivi e alle priorità consente invece di gestire i colli di bottiglia che emergono durante la giornata.
Una gestione di questo tipo richiede tuttavia la conoscenza in tempo reale del carico di lavoro di ogni processo, ovvero le code presenti, e le risorse allocate ai diversi processi. Sono queste informazioni di cui non sempre si dispone in maniera puntuale e strutturata, anche nel caso in cui si possa contare su un sistema software WMS, soprattutto per quanto riguarda la tracciabilità degli operatori.
Presso un’azienda nostra cliente che aveva la necessità di migliorare la gestione dei carichi di lavoro delle risorse in ottica di miglioramento del servizio è stato implementato uno strumento software ad hoc integrato all’interno del sistema WMS.
Attraverso un’interfaccia grafica a cruscotto lo strumento ha consentito di monitorare in tempo reale le code di lavoro e le risorse assegnate ai diversi processi/aree di magazzino, così da supportare il responsabile di magazzino nella gestione della riallocazione delle risorse in base alle effettive necessità del momento.
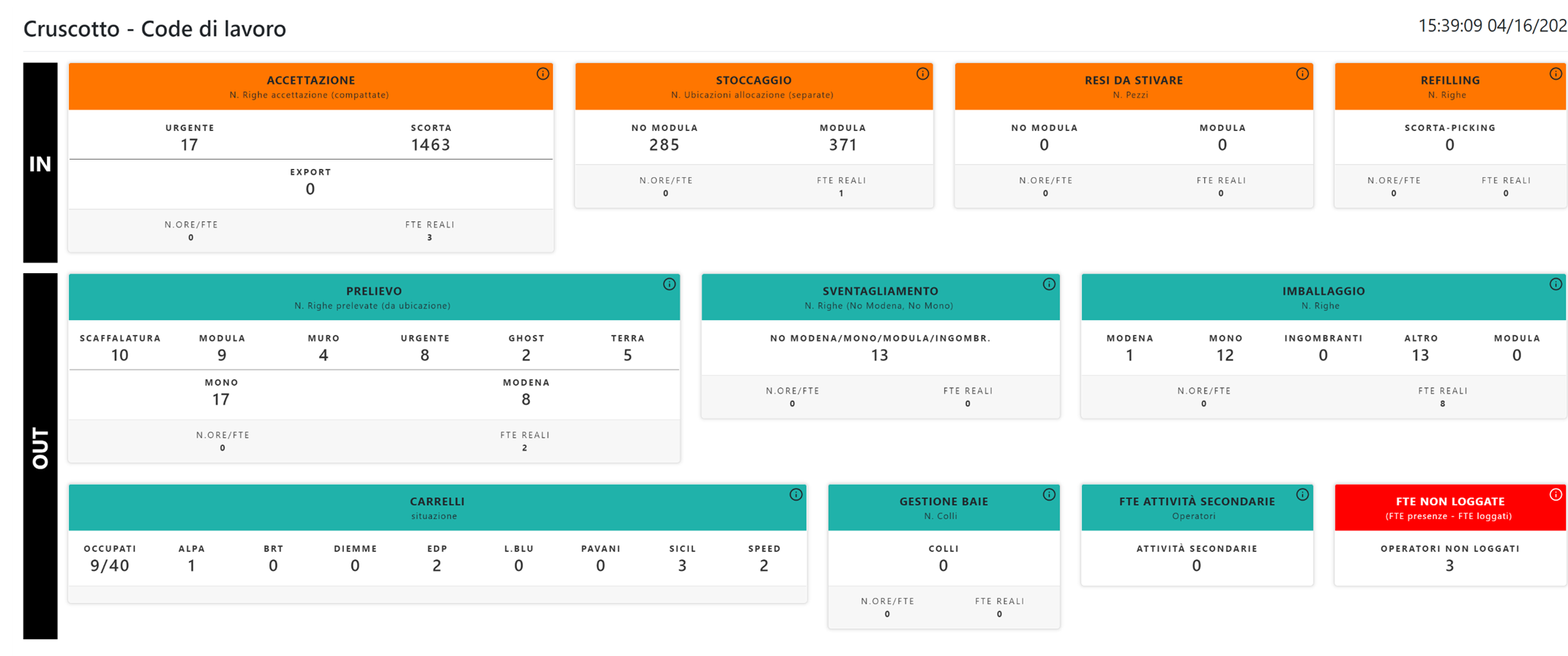
Questo strumento richiede la raccolta e l’elaborazione delle informazioni relative a:
- tracciamento degli operatori, ovvero chi è presente in una certa area di magazzino e che attività sta svolgendo.
Si tratta di un approccio innovativo per la logistica, che normalmente non ragiona con questa logica, tipica invece del mondo produttivo. In pratica si è esteso alla logistica un concetto che si trova normalmente nei sistemi MES (Manufacturing Execution System) dove gli operatori addetti alle macchine di produzione “dichiarano” quando cominciano e quando finiscono una determinata fase di lavoro.
Nel caso specifico, attraverso il proprio dispositivo mobile, l’operatore registra l’avvio e la conclusione di un’attività in un’area predefinita (accettazione, picking da scaffalatura, picking da automazione, imballaggio, etc.).
- carico di lavoro, misurabile attraverso un indicatore significativo e attendibile. Il KPI utilizzato in questo caso è dato dal n° righe applicato a tutti i processi di magazzino (n. righe in attesa di accettazione, n. righe di prelievo, n. righe da imballare, etc.), essendo un indicatore già gestito nel WMS.
Attraverso questo strumento software semplice e molto intuitivo l’azienda è riuscita a gestire con tempestività i colli di bottiglia, sincronizzando la capacità produttiva disponibile con il carico di lavoro effettivo e richiesto. Ha inoltre operato secondo le corrette priorità, con impatto sul livello di servizio (riduzione tempi di approntamento ed errori, puntualità) e sull’efficienza (riduzione tempi morti degli operatori, recupero attività in straordinario, riduzione degli spostamenti non mirati di personale, gestione in sequenza delle attività da svolgere).
In particolare, il responsabile di magazzino ha potuto disporre, in tempo reale, di tutte le informazioni necessarie per assegnare le risorse ai diversi processi in modo reattivo e preciso quando, in precedenza, le attività di assegnazione venivano svolte con schemi predefiniti e statici sulla base dell’esperienza e di informazioni parziali raccolte sul campo o dal WMS.
L’introduzione di un sistema di raccolta dati sulle attività svolte dagli operatori in un determinato lasso di tempo ha consentito inoltre di elaborare KPI puntuali e precisi relativi alla produttività delle diverse aree e dei processi di magazzino, fondamentali per una programmazione e un controllo ottimale dell’intero sistema logistico.
Riproduzione riservata©